Per- and polyfluoroalkyl substances have been the subject of high-profile lawsuits against chemical manufacturers 3M and DuPont de Nemours this year.
And yet, the use of PFAS, a group of synthetic, fluorine-based chemicals called fluorocarbons when discovered in the 1930s, went largely unregulated until the early 2000s. The toxicity of the substances, dubbed “forever chemicals” because of how slowly they break down over time, was even kept from the Environmental Protection Agency until the late 1990s.
But that is no longer the case. Dozens of U.S. cities and states have sued chemical manufacturers like 3M and DuPont, claiming the companies contaminated natural resources and endangered public health by adding forever chemicals to everything from cooking pans and cleaning supplies to firefighting gear. Studies have shown that exposure to certain levels of forever chemicals increases cancer risk, decreases fertility and damages the immune system, among other negative health effects.
But the chemicals are also a key component in various products across industries, used for their unique waterproof, durable and heat resistant qualities. Forever chemicals are in medical devices, aircrafts and semiconductors.
The renewed public attention on PFAS brings to light the chemicals’ winding history, a backstory that could help regulators and manufacturers alike better understand how the chemicals became so ubiquitous and how to keep the public safe from their harmful effects.
How PFAS evolved from unbranded chemicals to components in everyday items
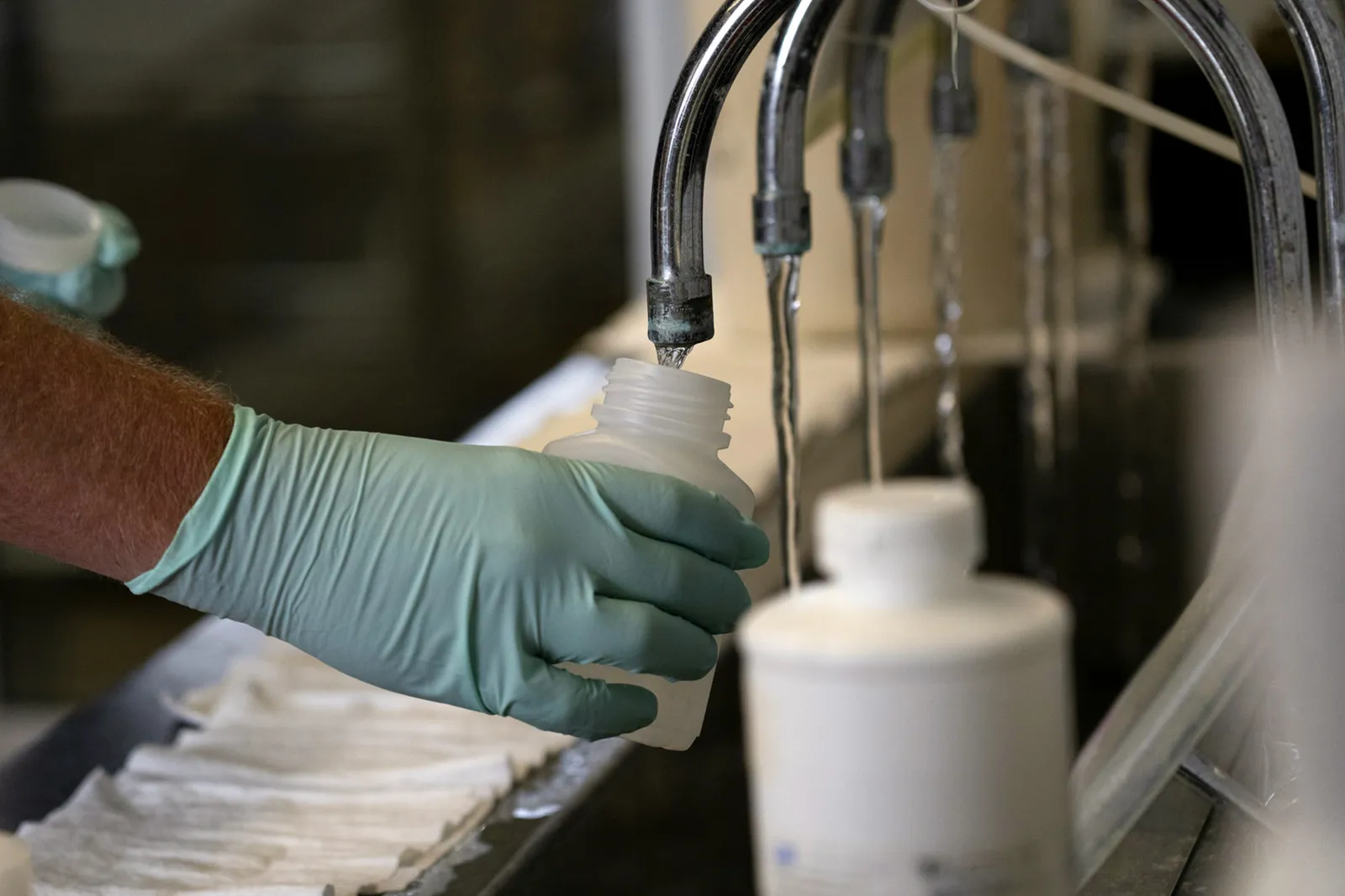
The genesis of forever chemicals
PFAS have existed for over 70 years. The chemical’s first form, polychlorotrifluoroethylene (PCTFE), was discovered by Fritz Schloffer and Otto Scherer in 1934 at the former German chemical conglomerate IG Farben.
PCTFE didn’t hit the commercial market until petroleum and pipe maker M.W. Kellogg, now known as KBR, commercialized it under the name Kel-F in the early 1950s. 3M bought Kel-F in 1957 and produced the chemical until 1996 when it sold the rights to Daikin Industries. The chemical is now produced under the name Neoflon PCTFE and used in semiconductors, chemicals and electronic components.
PCTFE was a precursor to a more prominent forever chemical. Polytetrafluoroethylene (PTFE), better known as Teflon, is popularized for its use in non-stick cookware, waterproof apparel and personal care products like nail polish.
However, Teflon was created by accident.
In 1936, Roy J. Plunkett, the soon-to-be inventor of Teflon, joined E.I. du Pont de Nemours & Co. after graduating from Ohio State University, the scientist wrote in his 1986 paper, “The History of Polytetrafluoroethylene: Discovery and Development.”
Plunkett was assigned by DuPont to develop a new alternative to existing fluorocarbon-based refrigerants. The company hoped to add to its patents for the lucrative chemicals, which, like their successor PFAS, were known for their use as lubricants, sealants and waterproofing.
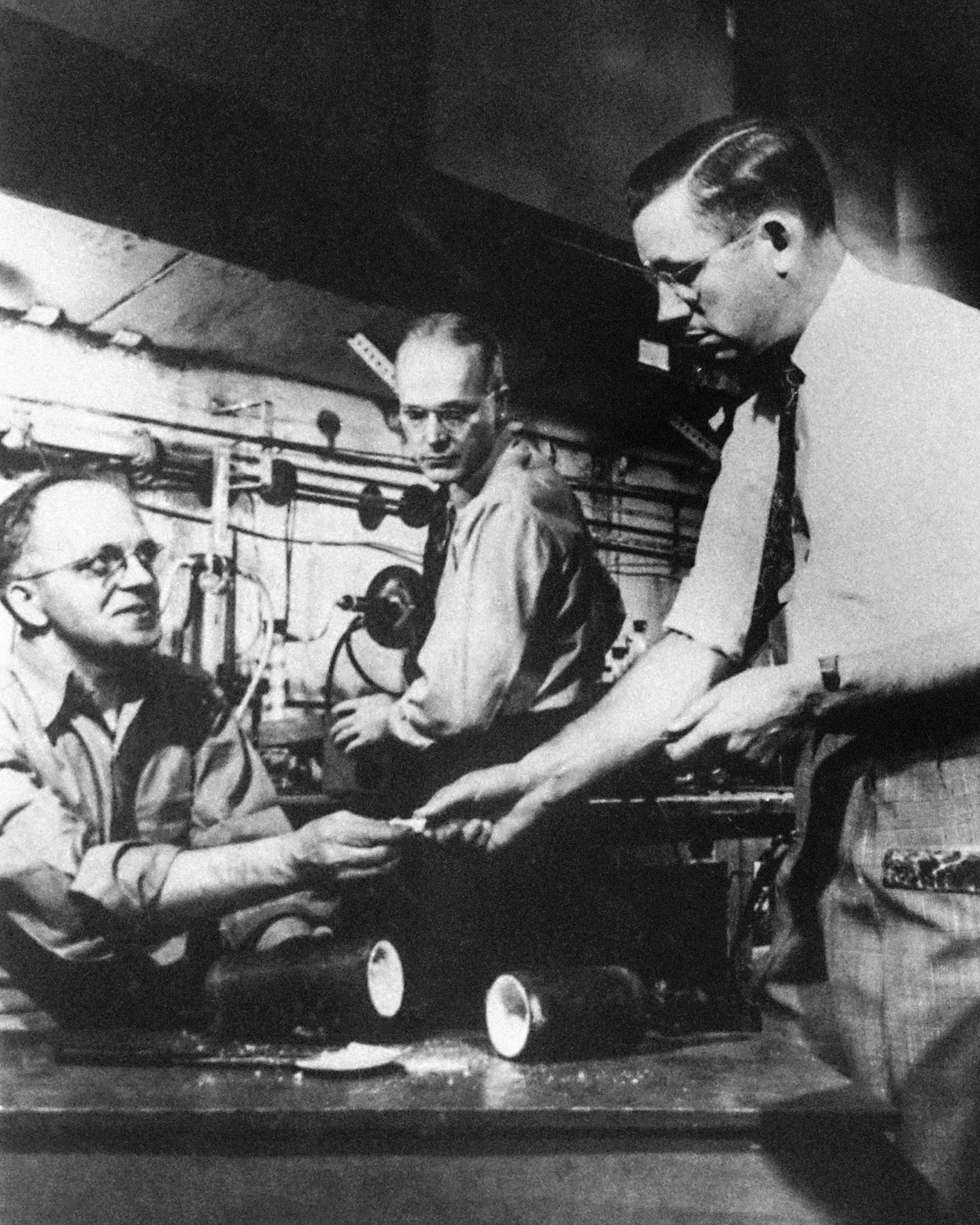
While working on the project in 1938, Plunkett and his assistant Jack Rebok discovered that a frozen, compressed sample of the fluorocarbon tetrafluoroethylene had spontaneously formed a white, waxy solid that would be dubbed PTFE and later trademarked as Teflon.
“The next question was, ‘What are you going to do with this stuff?’” Plunkett said in an interview with the Center for the History of Chemistry in 1986.
DuPont put Teflon to work as a component used in the Manhattan Project to build the atomic bomb during World War II. The chemical was used in material for gaskets and valves to hold toxic uranium hexafluoride in pipes at the project's uranium plant in Oak Ridge, Tennessee.
“It was believed that [PTFE] was going to be vital to this war project,” Malcolm Renfrew, a DuPont chemist who helped develop Teflon, said in an oral history.
Meanwhile, DuPont’s scientists began to study the new polymer. After the war, the chemical maker's scientists published academic papers on the various ways Teflon could be used and its capacity to withstand intense heat and "strenuous environments," Plunkett wrote in "The History of Polytetrafluoroethylene: Discovery and Development."
“The trick with PTFE is that it really took a lot of human beings and decades' worth of [research and development] and public money and [fused together] through the Manhattan Project to get to the Teflon that they eventually released,” said Rebecca Altman, a writer and sociologist on the history of chemistry, plastics, pollution and environmental legacy.
The early milestones of PFAS’ invention and spread
-
1934The first form of PFAS, polychlorotrifluoroethylene (PCTFE), is discovered by Fritz Schloffer and Otto Scherer at the former German chemical conglomerate IG Farben.
-
1938Roy J. Plunkett and Jack Rebok accidentally discover polytetrafluoroethylene (PTFE) when a frozen, compressed sample of the chemical fluorocarbon tetrafluoroethylene spontaneously forms a white, waxy solid.
-
1945DuPont trademarks PTFE as Teflon.
-
19453M, then known as the Minnesota Mining And Manufacturing Co., acquires the Simons Process from Joseph Simons, which allows the company to upscale the production of fluorochemicals and other types of PFAS.
-
1951
-
19533M scientists Patsy Sherman and Samuel Smith discover perfluorooctane sulfonic acid (PFOS), which would go on to be used as a component in a wide variety of products for years, including Scotchgard.
-
1954French engineer Marc Grégoire coats his wife’s cooking pans with Teflon. Two years later, Grégoire launches Tefal, a company that produces Teflon-coated cookware.
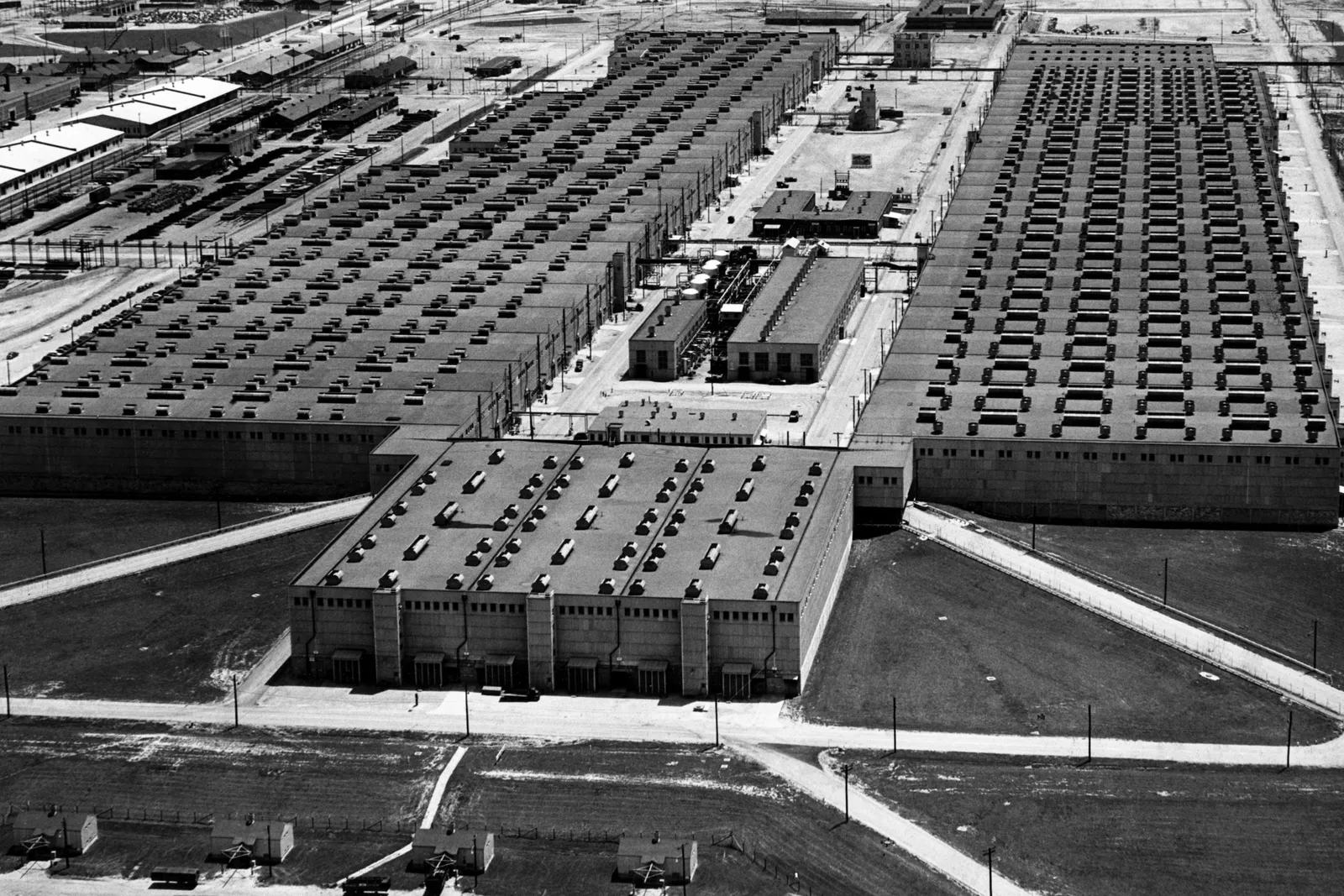
A shaky wartime start for PFAS
DuPont trademarked Teflon in 1945. While the federal government originally intended to build a plant specifically to manufacture DuPont's new substance for the war effort, the idea was scratched when researchers found PTFE challenging to work with, according to documents from the Atomic Energy Commission published in 1970.
“It just wasn't there yet,” Altman said.
Renfrew and his associates ran a pilot polymerization plant to produce PTFE at a DuPont site in Kearny, New Jersey, but the unit would run into problems and, ultimately, tragedy.
Three scientists died in DuPont’s organic chemicals section after being exposed to PFAS-containing chemicals, followed by two scientists from Renfrew’s lab who died due to an explosion at the Kearny site in 1944.
“The pilot plant stage is where processes are apt to run into accidents,” Renfrew said in an oral history. “Even at best, the hazards are there because you're doing new things with scaled-up quantities. And so we had our troubles.”
The incidents would serve as early signs of PFAS’ possible dangers.

The ‘Simons Process’ upscales manufacturing
Outside of its wartime applications, DuPont also wanted to produce Teflon on a commercial scale. Company scientists conducted studies on how to manufacture PTFE more broadly for other uses.
Around the same time DuPont was working on Teflon, a chemistry professor was producing liquid fluorocarbons at Pennsylvania State College, now Pennsylvania State University.
Joseph A. Simons worked on making “more complex fluorocarbons” by reacting materials with fluorine-containing compounds under milder conditions, which helped decrease the chances of an explosion or a fire when working with the chemicals, according to “A Chemical History of 3M.”
The process, named after its creator and dubbed the Simons Process, helped to upscale the production of fluorochemicals and other types of PFAS.
Like Teflon, the method was kept under wraps until after the war ended.
In 1945, 3M, then called the Minnesota Mining And Manufacturing Co., purchased the Simons Process from the scientist, which the manufacturer used to produce perfluorooctanoic acid, also known as PFOA. The chemical is another type of PFAS that resists heat, oil, stains, grease and water and is used in items such as stain resistant carpet and later, firefighting foam. It was also used to make Teflon.
At the time, DuPont was still trying to figure out how to work with Teflon. The company could still only produce the substance in small batches and it was expensive to make.
Eventually, the company approached 3M in search of a way to improve its own Teflon production process, said Altman. 3M offered DuPont PFOA, which helped the company successfully launch its Teflon production process.
“I don't know if it was the last brick in the wall, but it really was one of the final development breakthroughs when they kind of figured out the full chemistry of how to get this process up and running,” Altman said.
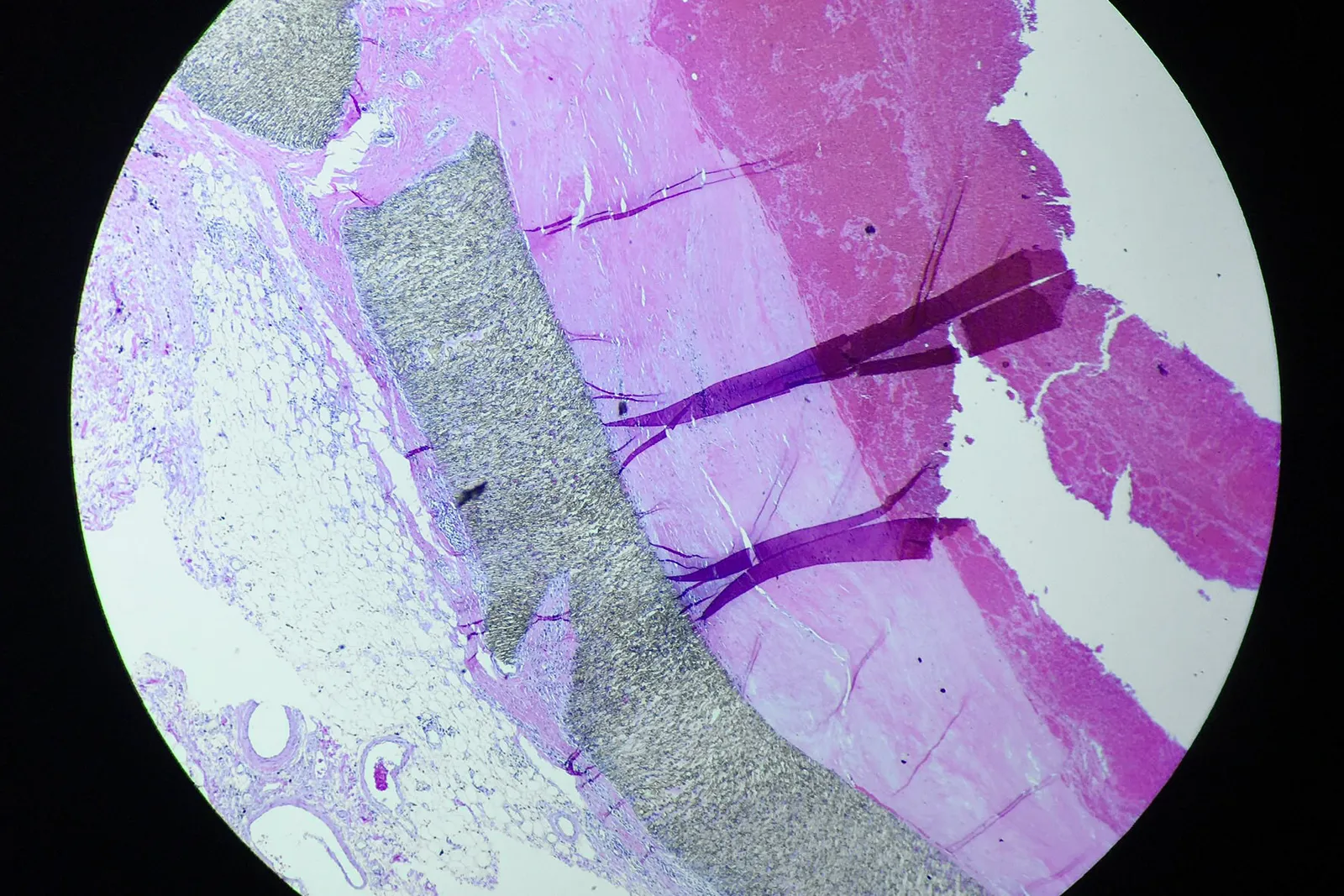
A revolutionary chemical takes off
When the war ended, publications such as Popular Mechanics wrote about fluorocarbons — a new chemical that promised to be revolutionary.
"Consider, for example, the possibility of a lifetime lubricant sealed into your car engine; a house paint that just plain refuses to permit your home to bum down; pots and pans that literally push away scorched foods; detergents so effective a grease monkey’s overalls will come clean in a few swishes," the magazine wrote in 1952.
In 1946, DuPont announced a new plastics manufacturing plant underway in Parkersburg, West Virginia. The facility began producing Teflon in 1951. Over the next several years, the company expanded the chemical's use into cookware, stain repellents in fabrics and textiles and industrial coatings.
Within 20 years of its initial discovery in 1934, PFAS in its many forms had gone from a laboratory accident, to an atomic bomb project component, to an ingredient in everyday household products.
“Products made from PTFE touches people in countless ways everyday from cookware to wire insulation and automobile gaskets; from soil repellants to dome roofs; from ski suits and space suits to lifesaving body parts,” Plunkett said in his 1986 paper.
“PTFE with its unusual properties and applications has become an integral part of the machinery that runs today's economy, affecting the fields of architecture, medicine, energy and environment conservation, fire protection, space travel, electronics and the military, among others," the scientist wrote.
News Graphics Developer Jasmine Ye Han also contributed to the story.