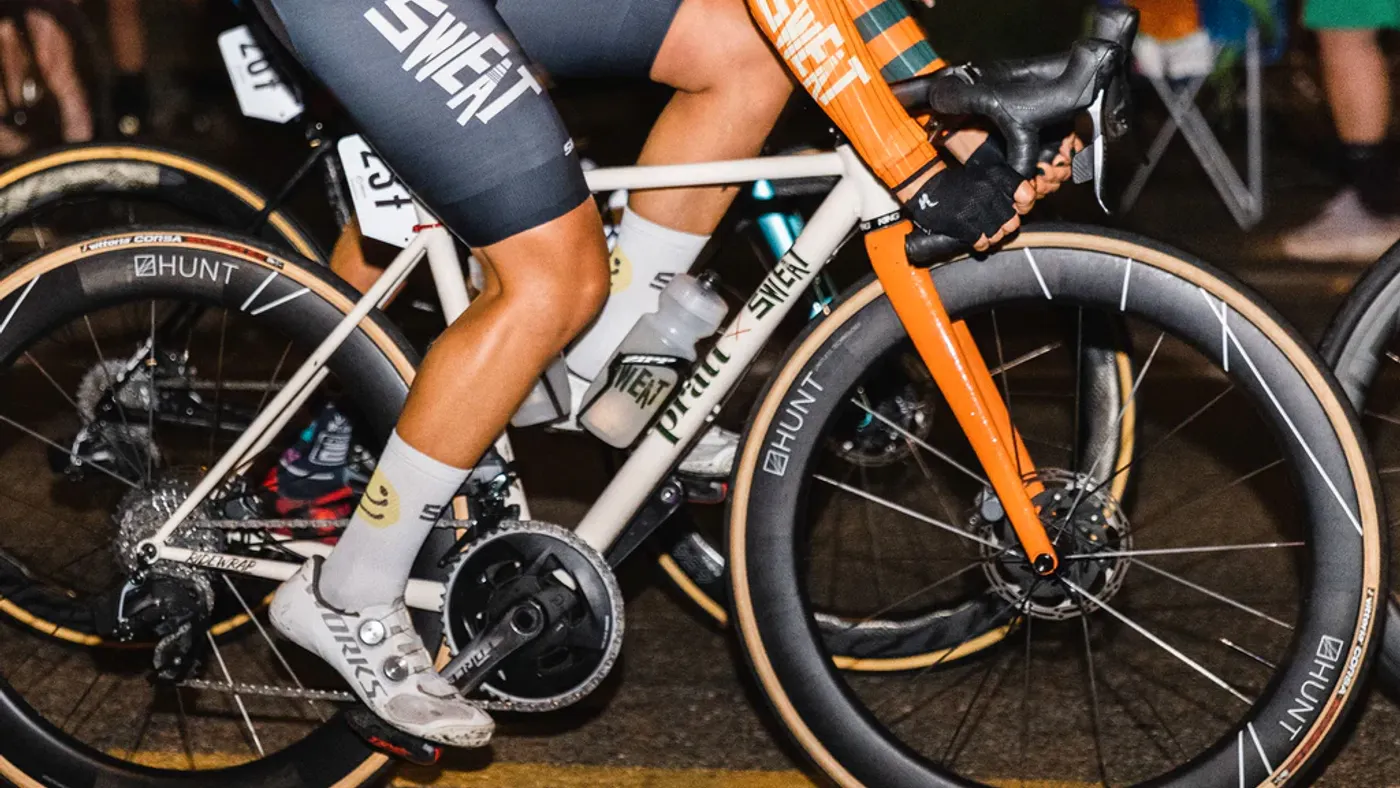
Additive manufacturing is pushing innovation in sportswear
In the world of sportswear, function typically outweighs form. But the limitations of traditional manufacturing practices have long stymied what’s possible with high-performing and innovative sports products.
“There’s this quote from Winston Churchill that I think about all the time in this regard — ‘First we design buildings, then the buildings design us,” said Michael Baker, global head of brand and communications at 3D-printing company Formlabs. “We make things with right corners or hard edges, not because they make better products, but because they’re easier to make at scale.”
3D manufacturing and other additive manufacturing techniques can offer ways to push past typical production restrictions when it comes to design, prototyping, cost and efficiency.
Quicker prototyping and more opportunities for innovation
For many manufacturers, the biggest advantage in using additive processes is in their potential to quickly prototype and iterate designs.
“Customers like TaylorMade [Golf], in the golf space, are asking us to quickly test out different form factors, geometries and weights of products,” Baker said. “They’ll try out 10 or 20 different shapes of a driver’s head, for example, before casting or molding.”
That’s traditionally a task that might have taken weeks or even months; 3D manufacturing can shave that time frame down to a single day, according to Baker.
“Instead of saying, ‘Oh, we can run this print today and then tomorrow we’ll have another version, and the next day we’ll have another version,’ you can actually change the workflow and say, ‘Today I’m going to come up with three different types and I’m going to give them to a focus group and they can see how these things change over the course of a day,” he said.
Shortening the prototyping time frame can also make product design more integral to the product development cycle, emboldening people to “think more creatively about what’s possible,” Baker added.

Enhancing small batch production
Improving efficiency across various steps of the manufacturing process is especially important for organizations like Varsity Brands and its subsidiary, BSN Sports, a manufacturer of sporting goods apparel for schools and leagues.
With its minimum order quantity ranging from a single unit to a dozen, Varsity Brands has found gaining efficiency in its small batch manufacturing production process an enormous challenge, according to Chief Innovation Officer Kurt Hagen.
Hagen said that his organization has primarily used 3D manufacturing to improve the sampling process. While before, one would have had to "order some very expensive molds that took a really long time to sample," Hagen says that 3D-printing allows the company to produce samples much faster.
“3D manufacturing allows you to look, feel, and touch [various samples], giving you more variety of choice,” Hagen says. “Before, you would have had to order some very expensive molds that took a really long time to sample.”
Unique shapes and constructions that enable high performance
Speed and efficiency aside, 3D manufacturing can also be a boon to high-volume manufacturers who want to innovate the construction of traditional sportswear, like shoes.
While working with New Balance, Formlabs helped design a new type of midsole shoe formed with resilient “lattice structures” that cradle different parts of the foot with varied support, boosting performance. Such nuanced design might not have been possible in a traditional manufacturing process, which would have required the production of various uniform layers that are then glued and stitched together.
Such unique shapes are made possible through the marriage of distinctive materials specifically developed for the 3D manufacturing process with the unconventional designs that additive manufacturing makes accessible.
“In the last five to eight years, there has been a huge explosion of elastomeric materials, heat-sensitive or fire-resistant, or extremely durable glass material — so things that actually mimic the properties of traditional manufacturing,” Baker said.
Baker added that materials are “half our business” and that Formlabs has more than 30 material science experts onsite to develop materials that fit every need — even FDA-cleared elastics used for sports guards.
How business owners can explore additive manufacturing
Speed is one of the most talked-about assets of 3D printing. But adopting 3D manufacturing processes might require some manufacturers to slow down and establish a digital foundation before exploring its opportunities, Hagen said.
“If a manufacturer is not digitally designing products, that’s going to be a ginormous barrier to entry,” Hagen said. “There’s a lot of use cases [with digital models] but you need to make sure you have the assets in place to allow them.”
The benefits of the technology is one of the most marked he’s experienced, though.
“I personally have not heard of anybody who’s gone down this path and did not realize the benefits,” Hagen said. “I have not heard from anybody that has made the jump and regretted it.”