As companies continue to invest billions of dollars into new U.S. manufacturing sites, employers are searching for the next generation of industry talent.
The issue is top of mind for many executives, who are increasingly looking for individuals ready for careers in emerging tech manufacturing, including in semiconductor, battery and EV production.
To close October's national manufacturing month, we spoke with Carolyn Lee, president and executive director of the National Association of Manufacturers' workforce development organization the Manufacturing Institute, on how companies can most effectively recruit and keep top talent at a time when the labor pool is still crunched.
Editor's note: This interview has been edited for length and clarity.
MFG Dive: What are the top recruitment and retention issues facing manufacturers?
LEE: We have a perception challenge first. Right now, I think we've got about 617,000 open jobs according to the most recent numbers from the [Bureau of Labor Statistics]. Coming out of the pandemic the first year, we were at about 800,000 open jobs every month. But to give you a baseline, going into the pandemic we were at about a half a million every month.
We have all these jobs and in recent months we've had a huge number of announcements of investment, of plants, we have lots of reporting about nearshoring, and then of course there's the Bipartisan Infrastructure bill and then the CHIPS Act. So there's a huge boom.
So all that's happening while we have a baseline of open jobs that we've been facing for a while.
First, we have to change perception. Then we've got to help people with skills, or the baseline skills that prepare them for manufacturing careers, and then we have to help recruit them and then retain them. So it's kind of the whole lifecycle.
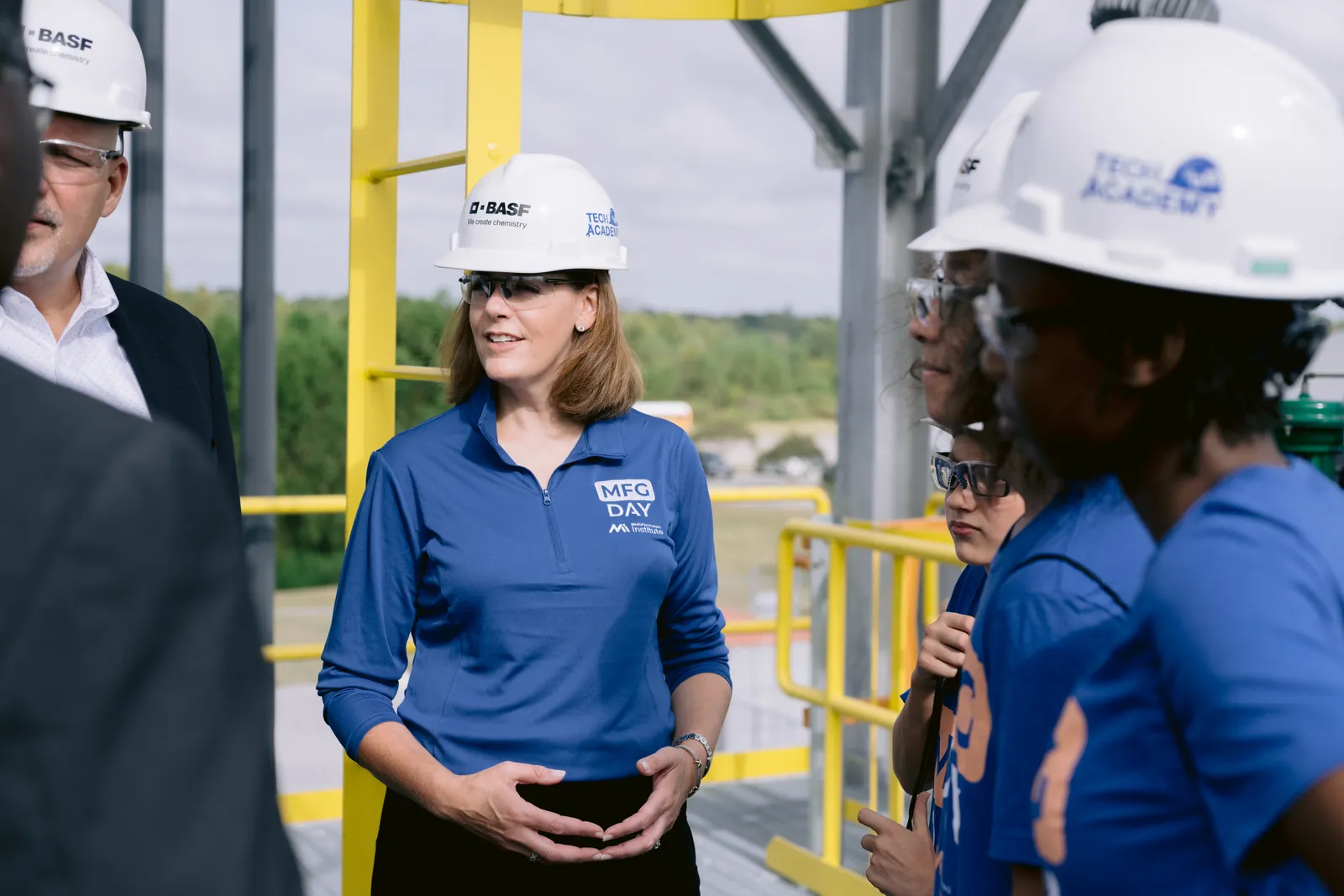
What are some of the top skills that companies are looking for in new recruits?
LEE: In any kind of job you're looking at in today's modern manufacturing, you need to have some basic skills – you need to be able to communicate, you need to be able to be trained, you need to be able to work on teams, you need to be able to problem solve and innovate, you need to be able to understand the importance of safety equipment and safety culture.
Then you have your more specific skill sets for the jobs that are open today. So, you know, to be fair, of that 617,000 open jobs that we have, that runs the gamut from HR and finance and marketing, all the way through the production floor, all the way through R&D. I always say, we need people who have six weeks of skills through certifications and six years or beyond, and there's a job for everyone across that entire continuum.
The Institute, through our various programs, we are training for some core manufacturing, high-need, widely applicable manufacturing core skill sets. Our Heroes MAKE America program trains certified logistics technician, certified production technicians and mechatronics [engineers], all of which is a short course certification.
Through the Federation for Advanced Manufacturing Education, we're training for global best, multi-skilled maintenance technicians through a federated apprenticeship model. That is training for those maintenance jobs that you need for all modern facilities where any automatic equipment, any 4.0 technology, any robotic equipment and other kinds of advanced manufacturing equipment is operating, you need maintenance techs, that is ubiquitous and universal.
What types of wages, benefits and opportunities should manufacturers offer to recruit and retain employees?
LEE: We have a study that we put out in May of 2022 that was looking at compensation, and what we found is of course pay and benefits matter. Manufacturing pays some of the highest wages across the economy. $98,000 I think is the average manufacturing wage, and that's you know, all job functions all across the U.S.
The other thing that matters is inclusion. MI launched our diversity and inclusion pillar of work at the beginning of 2020 to expand the work we've been doing for over a decade around bringing more women into the sector. George Floyd, of course, was murdered shortly after COVID began. And there was just a huge influx of questions about how do companies make sure that they're doing the right things on the D&I front?
Go now forward to 2022, we released this compensation paper and one of the things that was very loud and clear was that employees really valued bringing their whole selves to work, being able to feel included, that they are heard and seen in the workplace.
So yes, absolutely pay and benefits matter. But also things about, do you have close connections at the workplace? Do you feel like you can ask questions, raise ideas and be seen and heard?
And so companies doing things like employee resource groups and other kinds of culture-focused activities are key drivers of retention. So now expand that as you're looking at mentorship, having a mentor internally, having the ability to mentor others, being able to be an ambassador for your company.
"Absolutely pay and benefits matter. But also things about, do you have close connections at the workplace? Do you feel like you can ask questions, raise ideas and be seen and heard?"

Carolyn Lee
Manufacturing Institute President and Executive Director
How are you working to engage more populations across the U.S. in manufacturing?
LEE: The number one labor potential for the manufacturing sector is actually to close the gender gap. And that's why we have such a strong focus on gender and we're bringing more women into the sector.
If we close the gender gap by 10%, we would fill the entire number of open jobs. We're at 29% today, and the potential pool is of course, near 50%. It's really about how do we change the perception and bring more women in.
A huge potential labor pool for all of the economy, but particularly in manufacturing is the one in three Americans who have had exposure to the criminal justice system. And we've been doing work over the last two and a half years to help companies understand, how do you tap into this talent? How do you find a ready workforce, those who are ready to move to their next step?
By working with community based organizations, like we did a project with Goodwill being the training provider in the Atlanta region, where Goodwill identified those coming out of criminal justice involvement, helped them with some workforce readiness skills, and then we worked to help manufacturers come in and onboard those individuals and then train them critically, giving those individuals the support they need to be able to be successful in their careers.
What are some of the most difficult positions to fill in manufacturing?
LEE: I was talking to companies last week, we held our second annual workforce summit, and with those types of companies we talked about automation engineers and data science and computer science, all of those highly specialized roles are critical for manufacturing. There's a huge need for cybersecurity in the manufacturing sector.
But we also have a huge amount of demand for team leads and for innovation and R&D. So there's a huge range and that's why I really lean into talking about the production roles because I think people don't see them or understand them.
The engineering class everyone's like, "Oh, yeah, I've heard of that." But you know, there's just a huge amount of opportunity to come into in production and continue to progress and grow in a career